
Petromaster is the sole service provider for this service in the GCC, which is based on the detection of the Self Magnetic Leakage Fields (SMLF), arising in ferromagnetic and paramagnetic products on accumulations of high-density dislocations to detect high-Stress Concentration Zones (SCZ’s).
This technology can be used on contact and non-contact bases to access ferromagnetic piping and pipeline external and internal conditions. It can be used on bare, insulated, and buried piping. This technology coupled with RBI can be used to optimally improve OSI select locations for further monitoring.
Metal magnetic memory (MMM) is the residual magnetization in components and welded joints formed during their fabrication and/or operation. Most damage takes place in the stress concentration zones (SCZ). The SCZ are the locations of highest stresses as compared to average or reference (nominal) stress. The SCZ are the main sources of equipment damage. Corrosion, fatigue, and creeping are developed in the SCZ most intensively. Detection of the SCZ is very important for early diagnostics of fatigue damage and evaluation of equipment and structure lifetime.
The MMM method uses natural magnetization and after-effect displayed as the magnetic memory of metal to actual strains and structural changes in products and equipment metal.
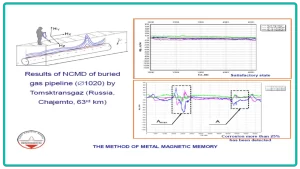
This technology after-effect which occurs as residual magnetization in components and welded joints formed during their fabrication and cooled down to ambient temperatures under interaction with weak magnetic fields or due to irreversible change of the local magnetization state of components in zones of stress concentration and damage under working.
This technology is covered in international standards including:
- ISO 24497-1:2007(E) Non-Destructive testing – Metal magnetic memory – Part 1: Vocabulary.
- ISO 24497-2:2007(E) Non-Destructive testing – Metal magnetic memory –Part 2: General Requirements.
- ISO 24497-3:2007(E) Non-Destructive testing – Metal magnetic memory – Part 3: Inspection of welded joints.
Applications of MMM
- Non-Contact Method of Inspection for buried Pipelines
- NCMD was developed using the specialized multi-channel highly sensitive flux gate sensors as a unit of TSC-type instrument. The main task is detection of potentially dangerous segments of buried pipelines by MMM technology. NCMD is based on distortions analysis of the magnetic field of the earth, conditioned by buried pipeline metal state including its stress-strained state.
Diagnostic of boiler and furnace tube
- Express method of vessels inspection
- Diagnostics of steam turbine blades
- Diagnostics of corrosion under insulation (CUI)
Advantages of MMM
- Allows for detection of impending failures of critical industrial equipment in the most dangerous stress concentration zones (SCZ).
- Contact Method is sensitive to microstructure degradation in the SCZ, therefore it allows detecting fatigue damages at initial stage of its development and propagation.
- Passive method (no magnetization induction is required).
- No special test surface preparation required.
- Saves money by eliminating the need for unnecessary full screening of lengthy pipelines by focusing detailed inspection on Stress Concentration Zones only.
Contact us for further information at info@petromaster-sa.com